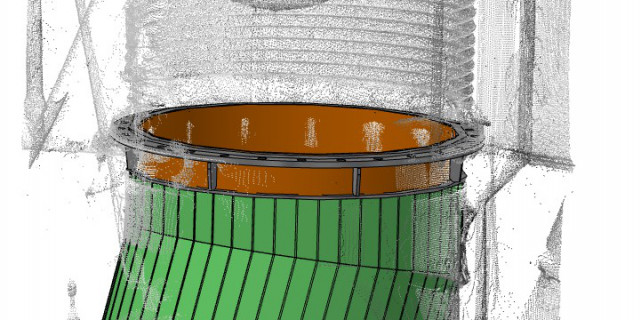
Inhaltsverzeichnis
-
Was kann die KSK Analyse Planung Design im Bereich der Schadensanalyse für Sie leisten?
- Ursachen erforschen.
- Befund aufnehmen.
- Untersuchung einleiten.
- Ergebnisse ableiten.
- Ihr Ansprechpartner (KSK)
- Ihr Ansprechparnter (StandZeit)
Was kann die KSK Analyse Planung Design im Bereich der Schadensanalyse für Sie leisten?
Ursachen erforschen.
Ihr Bauteil hat einen Schaden genommen. Sie konnten den Schaden zwar kurzfristig instandsetzen und dem Produktionsteam die Wiederaufnahme des Betriebs zusichern, aber wie geht es jetzt weiter? Wird ein ähnlicher Schaden an anderer Stelle ebenfalls auftreten? War die Reparaturmaßnahme ausreichend?
Die entscheidende Frage lautet: Was war die Ursache für den Schadensfall?
Bei der Ermittlung der Ursachen stehen Ihnen unsere Experten der KSK Analyse Planung Design gemeinsam mit unserem Partnerunternehmen StandZeit GmbH aus Coesfeld zur Seite. Die KollegInnen der StandZeit sind Spezialisten im Bereich werkstoffkundlicher Untersuchungen und verfügen unter anderem über jahrzehntelange Erfahrung in der Kraftwerks- und Müllverbrennungsbranche.
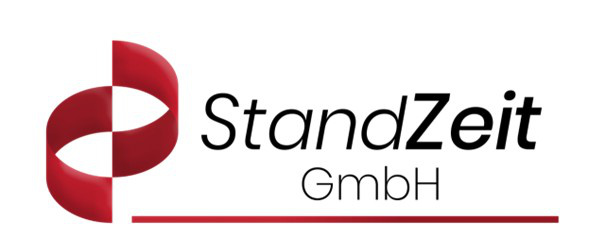
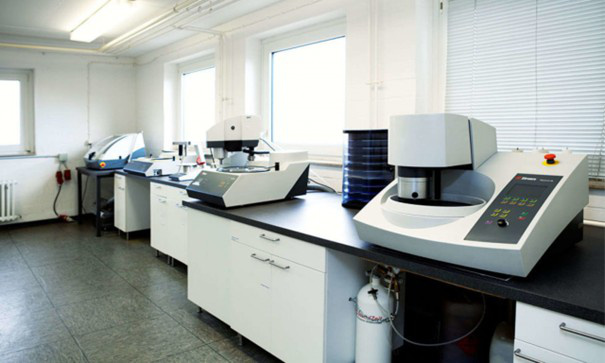
Befund aufnehmen.
Nach dem Auftreten eines Schadens sind für die Schadensursachenklärung unter anderem die drei folgenden Punkte zu beachten:
1.) Ermittlung des eigentlichen primären Schadensbereichs, der häufig von zahlreichen Sekundärschäden überlagert ist.
2.) Heraustrennen und Versand der schadhaften Stellen unter Anleitung unserer Experten.
3.) Bereitstellung von weiteren Informationen, wie z.B. Betriebsparameter oder Hinweise auf frühere Schäden.
In einigen Fällen ist die Befundaufnahme vor Ort durch unsere Experten sinnvoll, insbesondere dann, wenn bei dieser Gelegenheit noch weitere Untersuchungen an Nachbarbauteilen durchgeführt werden können.
Untersuchung einleiten.
Bei der Laboruntersuchung setzt StandZeit auf modernste Präparations- und Untersuchungsmethoden, die durch Partnerunternehmen ständig auf dem neuesten Stand der Technik gehalten werden.
Durch den Einsatz von halbautomatischen Präparationsmaschinen sind wir in der Lage, auch eine größere Anzahl an Proben in kurzer Zeit zu untersuchen. Mit modernsten Analysegeräten, wie z.B. der Rasterelektronenmikroskopie und der konfokalen Laser-Scanning-Mikroskopie, sind wir stets auf der Suche nach den Schadensmerkmalen. Sowohl in der Mikrostruktur als auch in der chemischen Zusammensetzung. So bleibt nichts im Verborgenen.
Ergebnisse ableiten.
Aus den Ergebnissen der Befundaufnahme vor Ort, den Informationen aus der Herstellung und der Konstruktion sowie der werkstoffkundlichen Untersuchung des Schadensbauteils im Werkstofflabor setzt sich das Schadensbild wie ein Puzzle Schritt für Schritt zusammen. Anhand der ermittelten Schadensmerkmale wird zuerst der Schadensmechanismus und anschließend die eigentlichen Schadensursachen abgeleitet.
Im Anschluss diskutieren wir gemeinsam mit Ihnen und unseren Experten die Ergebnisse der Untersuchungen und leiten Maßnahmen und Empfehlungen für den zukünftigen Betrieb Ihrer Bauteile ab.
Ihr Ansprechpartner (KSK)
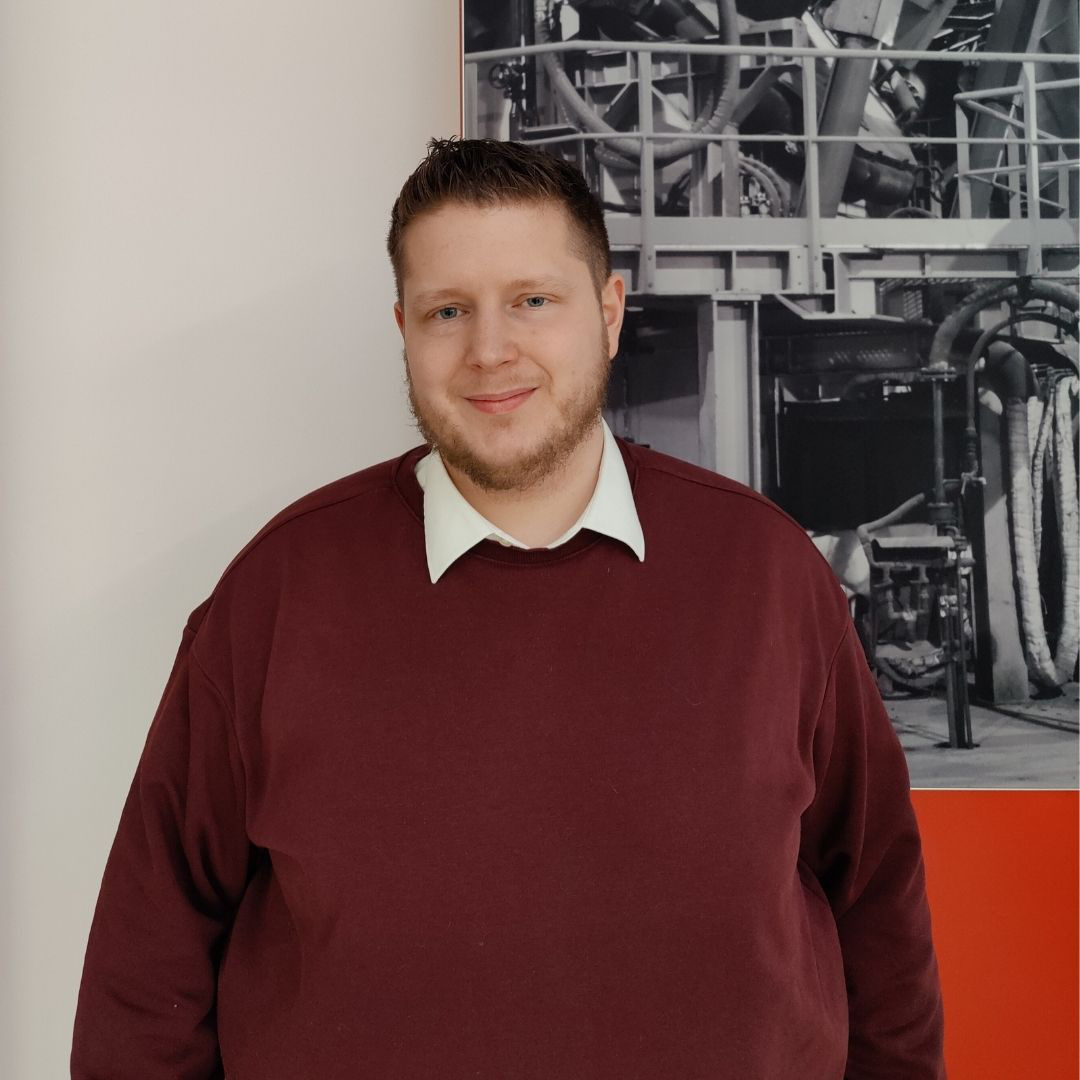
M.Sc. Björn Brüningk-Weißhar
Head of Engineering
Ihr Ansprechparnter (StandZeit)
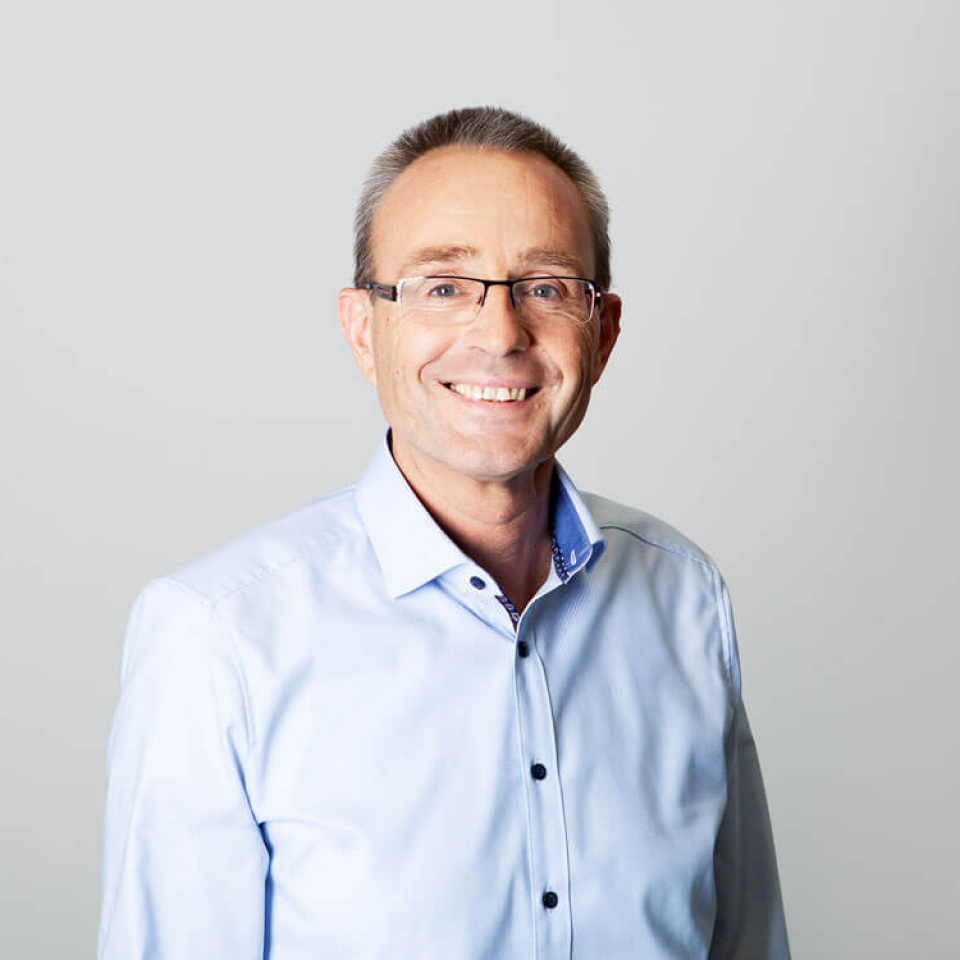
Dr. Gereon Lüdenbach
Geschäftsführer StandZeit GmbH
Was ist das Ziel einer Schadensanalyse?
Warum ist die Schadensanalyse wichtig?
In der heutigen industriellen Welt, in der die Integrität und Zuverlässigkeit von Bauteilen von entscheidender Bedeutung sind, spielt die Schadensanalyse eine zentrale Rolle. Eine effektive Schadensanalyse ist entscheidend, um das Versagen von Bauteilen zu verstehen und zukünftige Schäden zu vermeiden, was letztendlich zur Steigerung der Effizienz und Sicherheit von Produkten beiträgt. Dieser Leitfaden bietet einen tiefen Einblick in die Ziele, Methoden und Vorteile einer systematischen Schadensanalyse.
Das primäre Ziel einer Schadensanalyse besteht darin, die direkte und hypothetische Schadensursache eines Bauteils zu ermitteln und die Gründe für sein Versagen zu verstehen. Eine gründliche Schadensanalyse hilft, den Root Cause, also die primäre Ursache eines Schadens, zu identifizieren und somit gezielte Maßnahmen zu ergreifen, um ähnliche Schäden in der Zukunft zu vermeiden. Die Analyse bietet auch wertvolle Einblicke in die mikrostrukturellen Veränderungen, die durch konstruktive Mängel oder die erwartete Beanspruchung hervorgerufen werden.
Welche Vorteile bietet eine systematische Schadensanalyse?
Eine systematische Schadensanalyse bietet zahlreiche Vorteile. Sie ermöglicht eine präzise Ermittlung der Schadensursache und fördert das Wissensmanagement innerhalb eines Unternehmens, indem sie Daten und Erkenntnisse über frühere Schadensereignisse sammelt. Dies verbessert die Vergleichbarkeit verschiedener Schadensanalysen und unterstützt die technische Optimierung gefährdeter Bauteile. Letztlich trägt eine fundierte Analyse zur Verbesserung der Fertigung und zur Reduzierung von Ausfallzeiten bei.
Wie kann die Schadensanalyse helfen, zukünftige Schäden zu vermeiden?
Durch die Identifizierung der Schadensursache und das Verständnis der Bedingungen, die zu einem Schaden geführt haben, können Unternehmen präventive Maßnahmen ergreifen, die zukünftige Schäden verhindern. Dies kann beispielsweise durch den Tausch oder die technische Verbesserung von Bauteilen geschehen, sodass diese die erwartete Beanspruchung ertragen. Eine Schadensanalyse bietet somit nicht nur Einblicke in vergangene Ereignisse, sondern ist auch ein Werkzeug zur kontinuierlichen Verbesserung der Produktqualität und Zuverlässigkeit.
Wie verläuft der Ablauf einer Schadensanalyse?
Welche Schritte sind in einer systematischen Schadensanalyse enthalten?
Der Ablauf einer Schadensanalyse umfasst mehrere systematische Schritte. Zunächst wird der Schaden dokumentiert und eine hypothetische Schadensursache aufgestellt. Anschließend folgt die Untersuchung des Bauteils, um die mikrostrukturellen und materiellen Veränderungen zu analysieren. Die abschließende Schadensanalyse wird durch eine Bewertung der Untersuchungsergebnisse ergänzt, die oft mit der VDI-Richtlinie 3822 im Einklang steht, um die Vergleichbarkeit und Präzision der Analyse zu gewährleisten.
Wie wird eine Schadensursache ermittelt?
Die Ermittlung einer Schadensursache erfolgt durch eine Kombination aus visuellen Inspektionen, Werkstoffprüfungen und analytischen Methoden. Ziel ist es, die primäre und sekundäre Schadensursache zu identifizieren und das gesamte Schadensbild zu verstehen. Dieser Prozess beinhaltet oft die Untersuchung von Mikrostrukturen und die Analyse von Werkstoffen, um festzustellen, ob der Schaden durch Korrosion, Materialermüdung oder andere Faktoren verursacht wurde.
Welche Rolle spielt die VDI-Richtlinie 3822?
Die VDI-Richtlinie 3822 spielt oft eine zentrale Rolle im Rahmen der Schadensanalyse, da sie Standards und Leitlinien zur Durchführung einer systematischen und vergleichbaren Analyse bietet. Diese Richtlinie hilft Ingenieuren und Technikern, eine konsistente Methodik bei der Untersuchung und Bewertung von Schäden anzuwenden, was zu zuverlässigeren und nachvollziehbareren Ergebnissen führt.
Welche Methoden werden in der Schadensuntersuchung eingesetzt?
Welche Untersuchungsmethoden sind für metallische Werkstoffe geeignet?
Für metallische Werkstoffe werden in der Schadensuntersuchung insbesondere zerstörungsfreie Prüfmethoden angewandt, um die Integrität des Materials zu wahren. Zu den gängigen Methoden zählen die Röntgenfluoreszenzanalyse, die Elektronenmikroskopie und die Spektroskopie. Diese Techniken ermöglichen eine detaillierte Untersuchung der Materialzusammensetzung und der Mikrostrukturen, um mögliche Anomalien und Schäden zu identifizieren.
Wie wird die Werkstoffprüfung durchgeführt?
Die Werkstoffprüfung ist ein wesentlicher Bestandteil der Schadensanalyse und wird in der Regel in spezialisierten Laboren durchgeführt. Sie umfasst sowohl mechanische Tests, wie Zug- und Druckversuche, als auch chemische Analysen. Diese Tests helfen, die Festigkeit, Elastizität und Beständigkeit der Werkstoffe unter verschiedenen Bedingungen zu bestimmen, um Schwachstellen und potenzielle Schadensursachen zu erfassen.
Welche Techniken sind für die Ermittlung von Korrosionsschäden geeignet?
Zur Ermittlung von Korrosionsschäden werden spezifische Techniken wie die elektrochemische Impedanzspektroskopie und die Potenzialmessung eingesetzt. Diese Methoden helfen, die Korrosionsrate und die Schutzwirkung von Oberflächenbeschichtungen zu bestimmen. Durch gezielte Analysen können die Ursachen für Korrosionsschäden identifiziert und geeignete Gegenmaßnahmen entwickelt werden, um die Lebensdauer der Bauteile zu verlängern.
Wie können die Ergebnisse einer Schadensanalyse zur Vermeidung zukünftiger Schäden genutzt werden?
Welche Maßnahmen können ergriffen werden, um Schadensursachen zu vermeiden?
Um Schadensursachen zu vermeiden, können verschiedene Maßnahmen ergriffen werden, darunter die Anpassung von Design und Materialien, die Implementierung präventiver Instandhaltungsstrategien und die Überwachung von Betriebsbedingungen. Die Ergebnisse einer Schadensanalyse liefern wertvolle Informationen, die es ermöglichen, spezifische Schwachstellen zu adressieren und die Funktion des Bauteils zu verbessern.
Wie beeinflusst die Schadensanalyse die Funktion des Bauteils?
Die Schadensanalyse hat einen direkten Einfluss auf die Funktion des Bauteils, da sie es ermöglicht, potenzielle Schwachstellen zu identifizieren und zu beheben. Durch die Analyse können Designfehler korrigiert, Materialauswahl optimiert und Herstellungsprozesse angepasst werden, um die Leistung und Lebensdauer der Bauteile zu verbessern.
Wie kann die technische Optimierung gefährdeter Bauteile erfolgen?
Die technische Optimierung gefährdeter Bauteile erfolgt durch eine Kombination aus Designanpassungen, Materialverbesserungen und innovativen Fertigungstechniken. Eine gründliche Schadensanalyse liefert die notwendigen Daten, um gezielte Veränderungen vorzunehmen, die die Widerstandsfähigkeit und Zuverlässigkeit der Bauteile erhöhen. Durch kontinuierliche Überwachung und Anpassung können Unternehmen sicherstellen, dass ihre Produkte den höchsten Qualitäts- und Sicherheitsanforderungen entsprechen.
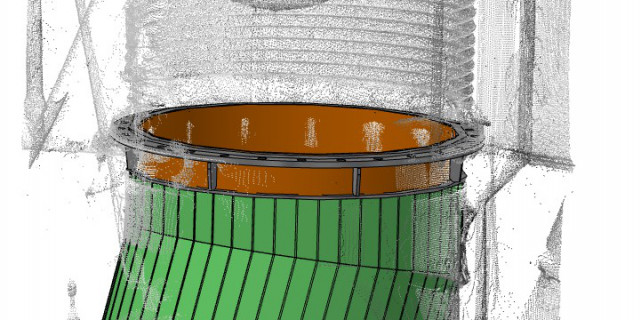

Analyse und Beratung
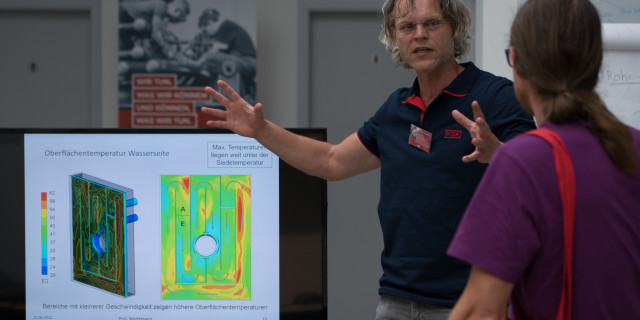
CFD Simulation
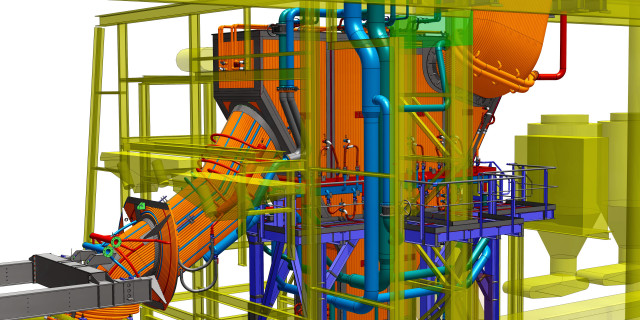
Concept Engineering
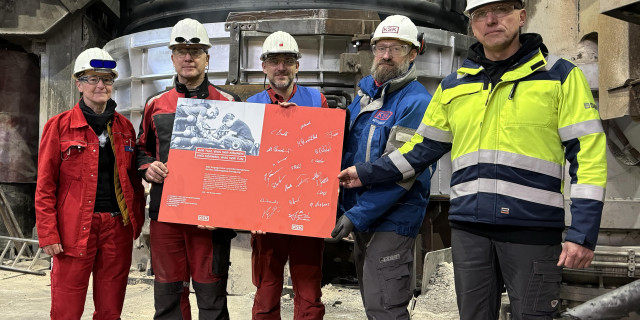
Inbetriebnahme von Anlagen
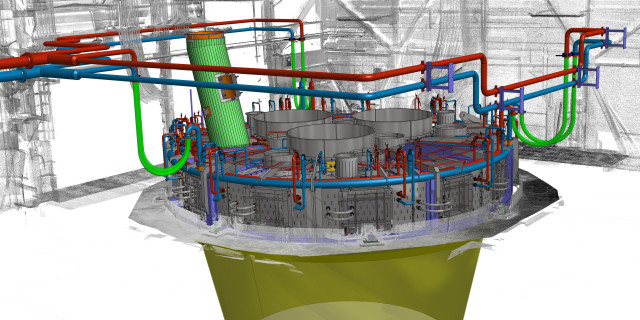
Konstruktionsbüro
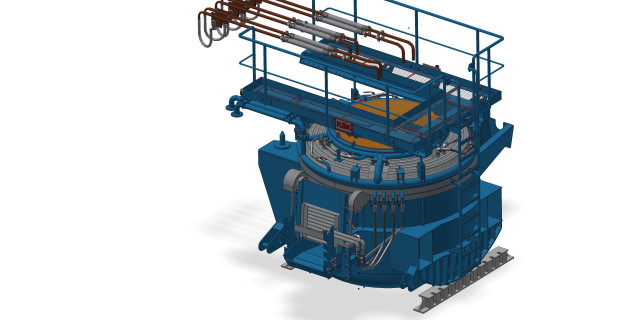
Reverse Engineering
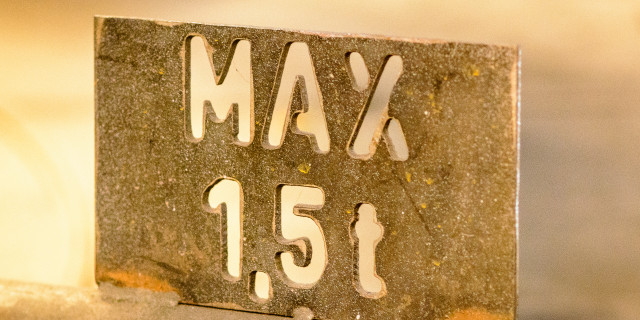
Safety Engineering
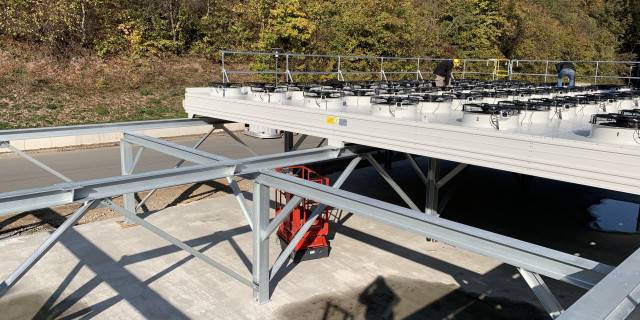
Stahlbau-Statik
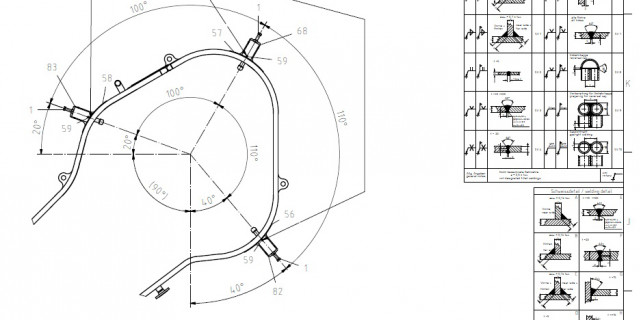
Technische Dokumentation
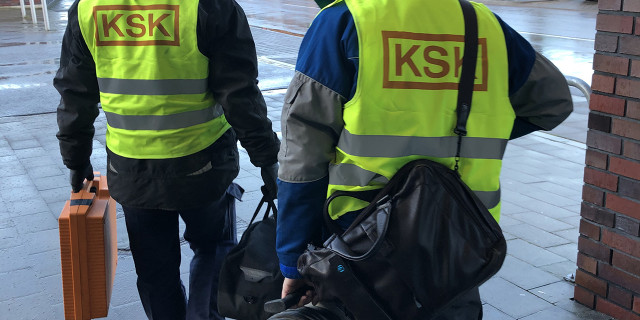
Projektmanagement
Inhaltsverzeichnis
- Q: Was ist das Ziel einer Schadensanalyse?
- Q: Wie läuft eine Schadensanalyse systematisch ab?
- Q: Welche Rolle spielt die VDI-Richtlinie 3822 bei Schadensanalysen?
- Q: Warum ist die Ermittlung der Schadensursache wichtig?
- Q: Welche Untersuchungsmethoden werden in der Schadensanalyse eingesetzt?
- Q: Wie hilft die Schadensanalyse bei der Vermeidung zukünftiger Schäden?
- Q: Was sind typische Ursachen für Schäden an Bauteilen?
- Q: Wie können die Erkenntnisse einer Schadensanalyse genutzt werden?
- Q: In welchem Rahmen wird eine Schadensanalyse durchgeführt?
Q: Was ist das Ziel einer Schadensanalyse?
A: Das Ziel einer Schadensanalyse ist es, die Schadensursache zu ermitteln und Maßnahmen zur Vermeidung zukünftiger Schäden zu entwickeln. Dies geschieht durch eine systematische Untersuchung und Bewertung des Schadens, um die Funktion des Bauteils wiederherzustellen und präventive Maßnahmen abzuleiten. Ein wesentlicher Bestandteil der Schadensanalyse ist die Datensammlung und -auswertung, die sowohl qualitative als auch quantitative Aspekte umfassen kann. Dazu gehören die Untersuchung der Betriebsbedingungen, die Analyse von Materialeigenschaften sowie die Bewertung von Konstruktions- und Fertigungsprozessen.
Im Rahmen der Untersuchung werden häufig Techniken wie visuelle Inspektionen, zerstörungsfreie Prüfverfahren, mikroskopische Analysen und chemische Analysen eingesetzt. Diese Methoden helfen, die Art und den Umfang des Schadens zu bestimmen und mögliche Ursachen wie Materialermüdung, Korrosion, Überlastung oder Herstellungsfehler zu identifizieren.
Sobald die Schadensursachen ermittelt sind, werden Maßnahmen zur Behebung und Vorbeugung erarbeitet. Diese können Designänderungen, Verbesserungen in der Materialauswahl, Anpassungen der Betriebsbedingungen oder die Einführung regelmäßiger Wartungs- und Überwachungsprogramme umfassen. Ziel ist es, die Zuverlässigkeit und Lebensdauer der Bauteile zu erhöhen und das Risiko zukünftiger Ausfälle zu minimieren.
Ein weiterer wichtiger Aspekt der Schadensanalyse ist die Dokumentation der Ergebnisse und die Kommunikation mit allen relevanten Stakeholdern. Dies stellt sicher, dass das gewonnene Wissen effektiv genutzt wird, um kontinuierliche Verbesserungen in der Produktqualität und der Betriebssicherheit zu erzielen.
Q: Wie läuft eine Schadensanalyse systematisch ab?
A: Eine systematische Schadensanalyse folgt typischerweise einem festgelegten Ablauf, der die Ermittlung der direkten Schadensursache, die Untersuchung des betroffenen Bauteils und die Bewertung der Einflussfaktoren umfasst. Dabei kommen verschiedene Untersuchungsmethoden wie Werkstoffprüfungen zum Einsatz. Eine systematische Schadensanalyse folgt typischerweise einem festgelegten Ablauf, der die Ermittlung der direkten Schadensursache, die Untersuchung des betroffenen Bauteils und die Bewertung der Einflussfaktoren umfasst. Dabei kommen verschiedene Untersuchungsmethoden wie Werkstoffprüfungen, zerstörungsfreie Prüfverfahren und mikroskopische Analysen zum Einsatz.
Der Prozess beginnt meist mit einer gründlichen visuellen Inspektion des Schadens, um erste Hinweise auf mögliche Ursachen zu erhalten. Anschließend können zerstörungsfreie Prüfverfahren, wie Ultraschall- oder Röntgenuntersuchungen, eingesetzt werden, um innere Defekte oder Materialfehler zu identifizieren, ohne das Bauteil weiter zu beschädigen.
Werkstoffprüfungen, wie Härteprüfungen oder Zugproben, liefern wertvolle Informationen über die mechanischen Eigenschaften des betroffenen Materials. Mikroskopische Analysen, einschließlich Rasterelektronenmikroskopie (REM) oder Lichtmikroskopie, ermöglichen eine detaillierte Untersuchung der Mikrostruktur des Materials und können Aufschluss über Korrosion, Risse oder Verformungen geben.
Ein wesentlicher Teil der Schadensanalyse ist auch die Betrachtung der Betriebsbedingungen und der Einsatzumgebung des Bauteils. Faktoren wie Temperatur, Druck, chemische Einflüsse oder mechanische Belastungen können erheblich zum Schadensereignis beitragen. Durch die Bewertung dieser Einflussfaktoren können Rückschlüsse gezogen werden, ob der Schaden durch Materialermüdung, Überlastung, chemische Korrosion oder andere Mechanismen verursacht wurde.
Letztendlich wird ein umfassender Bericht erstellt, der die Ergebnisse der Analyse zusammenfasst und Empfehlungen für präventive Maßnahmen gibt. Diese können Änderungen im Design, Materialwahl, Wartungsstrategien oder Betriebsbedingungen umfassen, um zukünftige Schäden zu vermeiden und die Lebensdauer des Bauteils zu verlängern.
Q: Welche Rolle spielt die VDI-Richtlinie 3822 bei Schadensanalysen?
A: Die VDI-Richtlinie 3822 bietet einen Rahmen für die systematische Durchführung von Schadensanalysen. Sie hilft, die Vergleichbarkeit verschiedener Schadensanalysen zu gewährleisten und unterstützt die Ermittlung der Schadensursachen durch standardisierte Verfahren. Die VDI-Richtlinie 3822 legt dabei besonderen Wert auf eine strukturierte Vorgehensweise, die von der Datenerfassung über die Schadensbeschreibung bis hin zur Ursachenanalyse reicht. Zu den wesentlichen Bestandteilen der Richtlinie gehören:
1. Dokumentation des Schadensfalls: Eine umfassende Sammlung aller relevanten Informationen, einschließlich der Umgebungsbedingungen, der Betriebsparameter und der Vorschäden.
2. Schadensbeschreibung: Eine detaillierte Beschreibung des Schadens, die unter anderem die Art des Schadens (z.B. Rissbildung, Korrosion, Verformung), die betroffenen Materialien und die Schadenslokalisation umfasst.
3. Analyse der Schadensursachen: Anwendung analytischer Methoden, um die physikalischen, chemischen oder mechanischen Ursachen des Schadens zu identifizieren. Dies kann durch Laboruntersuchungen, Simulationen oder andere technische Analysen geschehen.
4. Bewertung und Dokumentation der Ergebnisse: Zusammenstellung und Bewertung der gewonnenen Erkenntnisse, um klare Schlussfolgerungen über die Schadensursachen und mögliche Präventionsmaßnahmen zu ziehen.
5. Empfehlungen für Maßnahmen: Entwicklung von Handlungsempfehlungen, um zukünftige Schäden zu vermeiden. Dies kann die Modifikation von Konstruktionsmerkmalen, die Änderung von Materialien oder die Anpassung von Wartungsintervallen umfassen.
Die Anwendung der VDI-Richtlinie 3822 ist insbesondere in der Industrie von großer Bedeutung, da sie einen standardisierten Ansatz bietet, um die Zuverlässigkeit und Sicherheit von technischen Systemen zu verbessern. Durch die systematische Analyse von Schadensfällen können Unternehmen nicht nur die Ursachen für Ausfälle besser verstehen, sondern auch wertvolle Erkenntnisse gewinnen, um die Lebensdauer und Leistungsfähigkeit ihrer Produkte zu optimieren.
Q: Warum ist die Ermittlung der Schadensursache wichtig?
A: Die Ermittlung der Schadensursache ist entscheidend, um gezielte Maßnahmen zur Vermeidung zukünftiger Schäden treffen zu können. Nur durch das Verständnis, warum ein Schaden aufgetreten ist, können präventive Maßnahmen effektiv geplant und umgesetzt werden. Die Analyse der Schadensursache ermöglicht es, Schwachstellen im System aufzudecken und diese gezielt anzugehen. Dabei ist es wichtig, alle relevanten Faktoren zu berücksichtigen, die zu dem Schaden beigetragen haben könnten. Dies umfasst sowohl technische Aspekte als auch menschliche Fehler oder organisatorische Mängel.
Um eine gründliche Untersuchung durchzuführen, können verschiedene Methoden zum Einsatz kommen, wie zum Beispiel die Fehlermöglichkeits- und Einflussanalyse (FMEA), die Ursachen-Wirkungs-Diagramme oder die 5-Why-Methode. Diese Ansätze helfen dabei, die zugrunde liegenden Ursachen systematisch zu identifizieren und zu bewerten.
Sobald die Ursachen klar definiert sind, können konkrete Maßnahmen entwickelt werden, um ähnliche Vorfälle in der Zukunft zu verhindern. Dazu gehört möglicherweise die Verbesserung von Prozessen, die Schulung von Mitarbeitern oder die Investition in neue Technologien.
Es ist auch entscheidend, dass die gewonnenen Erkenntnisse dokumentiert und mit allen relevanten Stakeholdern geteilt werden. Nur so kann sichergestellt werden, dass das gesamte Unternehmen von den Erkenntnissen profitiert und eine kontinuierliche Verbesserung stattfindet. Langfristig trägt ein solcher Ansatz nicht nur zur Schadensvermeidung bei, sondern stärkt auch die Widerstandsfähigkeit und Effizienz der Organisation insgesamt.
Q: Welche Untersuchungsmethoden werden in der Schadensanalyse eingesetzt?
A: In der Schadensanalyse kommen verschiedene Untersuchungsmethoden zum Einsatz, darunter die Analyse von Mikrostrukturen, Werkstoffprüfungen und Korrosionsuntersuchungen. Diese Methoden helfen, die Schadensursachen gezielt zu ermitteln und das Versagen von Bauteilen zu verhindern. In der Schadensanalyse kommen verschiedene Untersuchungsmethoden zum Einsatz, darunter die Analyse von Mikrostrukturen, Werkstoffprüfungen und Korrosionsuntersuchungen. Diese Methoden helfen, die Schadensursachen gezielt zu ermitteln und das Versagen von Bauteilen zu verhindern.
Ein weiterer wichtiger Aspekt der Schadensanalyse ist die Fraktographie, bei der die Bruchflächen von beschädigten Bauteilen untersucht werden. Durch die detaillierte Betrachtung der Bruchoberflächen können Rückschlüsse auf die Art der Belastung und das Versagensverhalten des Materials gezogen werden. Dies ist besonders hilfreich, um zwischen sprödem und duktilen Bruchverhalten zu unterscheiden.
Zusätzlich spielt die chemische Analyse eine bedeutende Rolle. Durch die Untersuchung der Materialzusammensetzung und der Identifizierung von Verunreinigungen oder ungewollten Phasen können potenzielle Schwachstellen im Material aufgedeckt werden. Diese Erkenntnisse sind entscheidend, um Verbesserungen im Herstellungsprozess oder in der Materialauswahl vorzunehmen.
Die zerstörungsfreie Prüfung (ZfP) ist ebenfalls ein wesentlicher Bestandteil der Schadensanalyse. Techniken wie Ultraschallprüfung, Röntgenuntersuchung oder Magnetpulverprüfung ermöglichen es, innere Defekte zu erkennen, ohne das Bauteil zu beschädigen. Diese Methoden sind besonders nützlich für die regelmäßige Inspektion und Wartung von sicherheitskritischen Komponenten.
Zusammengefasst bieten diese Untersuchungsmethoden wertvolle Einblicke in die Ursachen von Schäden und tragen dazu bei, die Lebensdauer und Zuverlässigkeit von Bauteilen zu erhöhen. Durch die systematische Anwendung dieser Techniken können Ingenieure verbesserte Designs entwickeln und die Sicherheit in verschiedenen Industriezweigen gewährleisten.
Q: Wie hilft die Schadensanalyse bei der Vermeidung zukünftiger Schäden?
A: Die Schadensanalyse hilft, durch die gewonnenen Erkenntnisse gezielte Maßnahmen zur Prävention weiterer Schäden zu entwickeln. Durch den Austausch oder die Anpassung gefährdeter Bauteile können zukünftige Schadensereignisse vermieden werden. Zusätzlich ermöglicht die Schadensanalyse eine kontinuierliche Verbesserung der bestehenden Systeme und Prozesse. Durch die Identifikation von Schwachstellen und Risikofaktoren können Unternehmen proaktiv Maßnahmen ergreifen, um die Zuverlässigkeit und Langlebigkeit ihrer Produkte oder Anlagen zu erhöhen. Dies führt nicht nur zu einer Reduzierung der Instandhaltungskosten, sondern auch zu einer erhöhten Kundenzufriedenheit und einem besseren Ruf des Unternehmens.
Ein weiterer Vorteil der Schadensanalyse ist die Möglichkeit, aus vergangenen Fehlern zu lernen und das erworbene Wissen in die Entwicklung neuer Produkte einfließen zu lassen. Somit trägt die Analyse nicht nur zur Vermeidung von Schäden bei, sondern auch zur Innovationsförderung und zur nachhaltigen Optimierung der Produktqualität.
Insgesamt stellt die Schadensanalyse ein wichtiges Instrument im Qualitätsmanagement dar, das Unternehmen dabei unterstützt, wettbewerbsfähig zu bleiben und sich langfristig am Markt zu behaupten.
Q: Was sind typische Ursachen für Schäden an Bauteilen?
A: Typische Schadensursachen an Bauteilen können konstruktive Mängel, unzureichende Fertigungsprozesse, Überbeanspruchung oder Korrosion sein. Eine systematische Schadensanalyse kann die primären und sekundären Schadensursachen ermitteln. und hilft dabei, gezielte Maßnahmen zur Schadensvermeidung zu entwickeln. Dabei werden verschiedene Analysemethoden eingesetzt, um die Fehlerursachen zu identifizieren. Zu den häufig genutzten Methoden gehören visuelle Inspektionen, Materialanalysen, zerstörungsfreie Prüfverfahren sowie computergestützte Simulationen.
Ein wichtiger Schritt in der Schadensanalyse ist die genaue Dokumentation des Schadensbildes und der Umgebungsbedingungen. Dies beinhaltet die Erfassung von Temperatur, Feuchtigkeit, Belastungshistorie und anderen relevanten Faktoren, die zur Schadensentwicklung beigetragen haben könnten.
Nach der Ermittlung der Schadensursachen können entsprechende Korrekturmaßnahmen implementiert werden. Dazu zählen etwa die Optimierung des Designs, die Verbesserung der Materialauswahl, die Anpassung der Fertigungsverfahren oder der Einsatz von Schutzbeschichtungen gegen Korrosion. Zudem können regelmäßige Wartungs- und Inspektionsintervalle festgelegt werden, um zukünftige Schäden frühzeitig zu erkennen und zu verhindern.
Letztendlich trägt eine gründliche Schadensanalyse nicht nur zur Verlängerung der Lebensdauer von Bauteilen bei, sondern auch zur Erhöhung der Sicherheit und Wirtschaftlichkeit von Anlagen und Systemen.
Q: Wie können die Erkenntnisse einer Schadensanalyse genutzt werden?
A: Die Erkenntnisse einer Schadensanalyse können zur Verbesserung des Wissensmanagements und zur Optimierung der Fertigungsprozesse genutzt werden. Durch die systematische Auswertung der gewonnenen Daten können Unternehmen ihre Produkte und Prozesse kontinuierlich verbessern. Die Ergebnisse der Schadensanalyse bieten wertvolle Einblicke in Schwachstellen und Ineffizienzen innerhalb der bestehenden Systeme. Durch die Identifikation häufiger Fehlerquellen können gezielte Maßnahmen ergriffen werden, um die Qualität der Produkte zu erhöhen und die Produktionskosten zu senken. Zudem ermöglicht die Analyse eine bessere Vorhersage potenzieller Risiken, was zu einer proaktiveren Herangehensweise bei der Produktentwicklung führt.
Ein weiterer Vorteil der Schadensanalyse ist die Förderung einer Lernkultur innerhalb des Unternehmens. Mitarbeiter können aus den Ergebnissen lernen und diese Erkenntnisse in ihre tägliche Arbeit integrieren. Dies stärkt nicht nur das individuelle Wissen, sondern trägt auch zur kollektiven Intelligenz der Organisation bei.
Darüber hinaus kann die Schadensanalyse die Grundlage für Innovationen bilden. Indem Unternehmen verstehen, warum und wie Fehler auftreten, können sie neue, verbesserte Lösungen entwickeln, die nicht nur bestehende Probleme beheben, sondern auch neue Marktanforderungen erfüllen. So wird die Schadensanalyse zu einem integralen Bestandteil eines umfassenden Qualitätsmanagementsystems, das langfristig zum Erfolg und zur Wettbewerbsfähigkeit des Unternehmens beiträgt.
Q: In welchem Rahmen wird eine Schadensanalyse durchgeführt?
A: Eine Schadensanalyse wird typischerweise im technischen Rahmen durchgeführt, insbesondere wenn ein Bauteil das erwartete Beanspruchungsniveau nicht erträgt oder versagt. Der Ablauf einer Schadensanalyse wird abschließend dokumentiert, um zukünftige Präventionsstrategien zu entwickeln. Eine Schadensanalyse wird typischerweise im technischen Rahmen durchgeführt, insbesondere wenn ein Bauteil das erwartete Beanspruchungsniveau nicht erträgt oder versagt. Der Ablauf einer Schadensanalyse wird abschließend dokumentiert, um zukünftige Präventionsstrategien zu entwickeln.
Der erste Schritt in einer Schadensanalyse besteht in der Datensammlung. Hierbei werden alle relevanten Informationen über das versagte Bauteil, die Betriebsbedingungen und die Umstände des Versagens gesammelt. Dazu gehören technische Spezifikationen, Betriebsprotokolle, Wartungshistorien und Umweltbedingungen.
Anschließend erfolgt eine visuelle Inspektion des Bauteils, um erste Hinweise auf die Versagensursache zu identifizieren. Dabei werden Beschädigungen, Risse, Verfärbungen oder Verformungen dokumentiert. Oft werden ergänzend auch zerstörungsfreie Prüfmethoden wie Röntgenaufnahmen oder Ultraschalluntersuchungen eingesetzt, um verdeckte Schäden aufzudecken.
Nach der visuellen Inspektion wird eine detaillierte Materialanalyse durchgeführt. Diese kann chemische Analysen, metallographische Untersuchungen und mechanische Tests umfassen. Ziel ist es, Materialfehler, wie z.B. Einschlüsse, Korrosion oder unerwartete Materialermüdung, zu identifizieren.
Parallel dazu wird eine Ursachenanalyse durchgeführt, um die genauen Gründe für das Versagen zu ermitteln. Methoden wie die Fehlerbaumanalyse (Fault Tree Analysis) oder die Fehler-Möglichkeits- und Einfluss-Analyse (FMEA) können dabei helfen, systematisch mögliche Versagensursachen zu identifizieren und zu bewerten.
Abschließend werden alle Ergebnisse zusammengetragen und in einem Bericht dokumentiert. Dieser Bericht enthält nicht nur die identifizierte Versagensursache, sondern auch Empfehlungen zur Verbesserung von Design, Materialwahl, Fertigungsprozessen oder Wartungsstrategien, um zukünftige Schäden zu vermeiden.
Die Erkenntnisse aus der Schadensanalyse fließen in die Entwicklung von Präventionsstrategien ein, die darauf abzielen, die Zuverlässigkeit und Lebensdauer von Bauteilen zu erhöhen. Dazu gehören unter anderem die Einführung verbesserter Qualitätskontrollen, die Anpassung von Betriebsrichtlinien oder die Schulung von Personal im Hinblick auf frühzeitige Erkennung von Anzeichen für potenzielle Ausfälle.
Ihr Ansprechpartner (KSK)
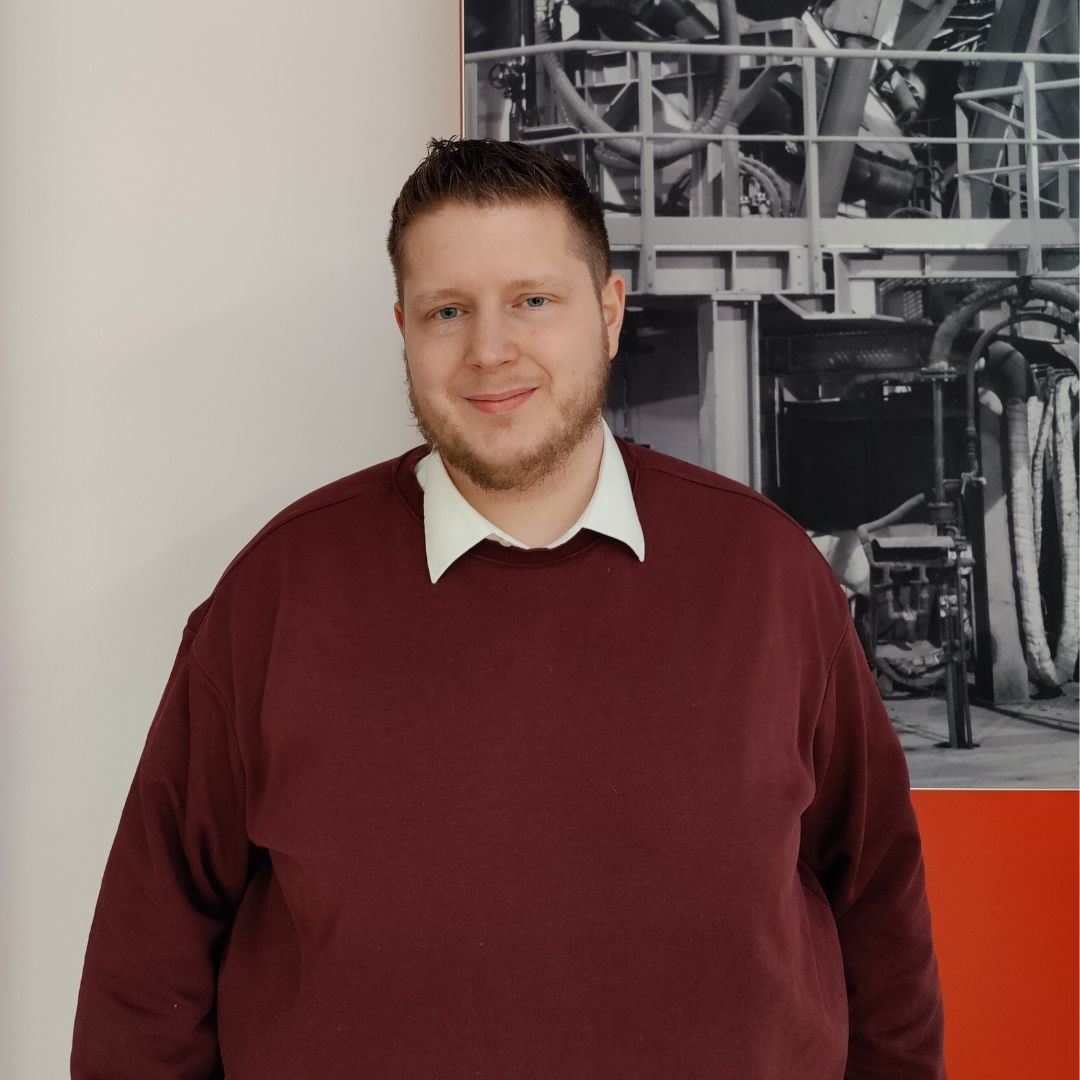
M.Sc. Björn Brüningk-Weißhar
Head of Engineering
Ihr Ansprechparnter (StandZeit)
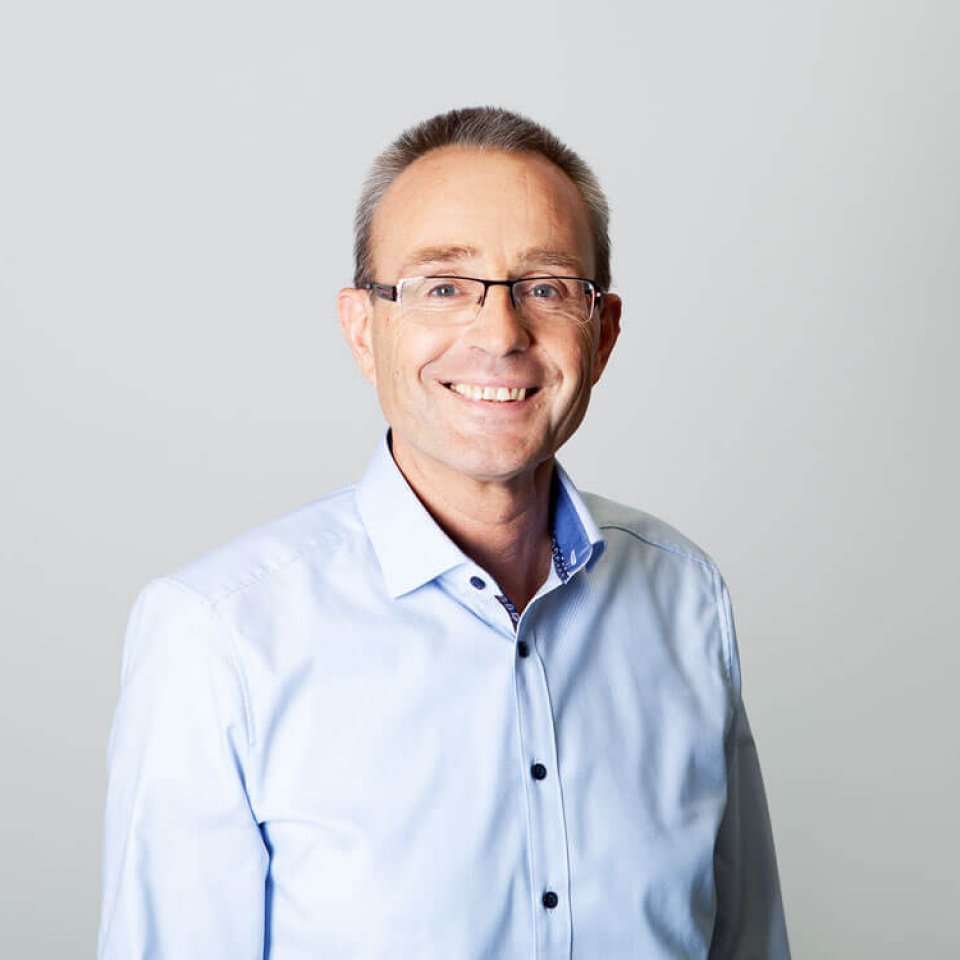
Dr. Gereon Lüdenbach
Geschäftsführer StandZeit GmbH